Smart manufacturing technologies change how industries operate. These technologies, forming the backbone of the ‘smart factory,’ enhance processes through manufacturing automation software, data analysis, and interconnected systems. They enable real-time decision-making, increase efficiency, and reduce waste.
Across various sectors, smart manufacturing technologies have a profound impact. For instance, BMW already has over 200 AI applications in production to reduce unnecessary repair and waste. In the aerospace sector, companies like Boeing focus on automation aimed at a 10 times reduction in process time for certain components due to advanced manufacturing technologies.
The cutting-edge smart manufacturing tools are transforming traditional production processes, introducing unprecedented efficiency, productivity, and adaptability. Our article explores the concept of smart manufacturing, its impact on various industries, the core ten technologies, and the future trends shaping this exciting field.
What Is Smart Manufacturing
Smart manufacturing is an advanced approach to production that takes advantage of technology, data, and industrial automation to positively affect efficiency and flexibility in processes. Central to this concept is the smart factory, an environment where interconnected systems and intelligent machines work seamlessly to optimize production. The components of smart factories represent a significant shift from the old practices to automated manufacturing, emphasizing data-driven decision-making and real-time responses to market demands.
Examples of industries adopting smart manufacturing practices are not limited to automotive and aerospace. Companies within the consumer electronics manufacturing industry, like Samsung, are adopting advanced technologies such as robotics and artificial intelligence to boost production, improve product quality, and drive innovation in the development of next-generation electronic devices.
Construction firms, such as Caterpillar, also lead in advanced technologies. They are incorporating drones, GPS technology, and AI-driven construction equipment for improved project management, safety, and overall efficiency on construction sites.
Levels of a Smart Factory Evolution
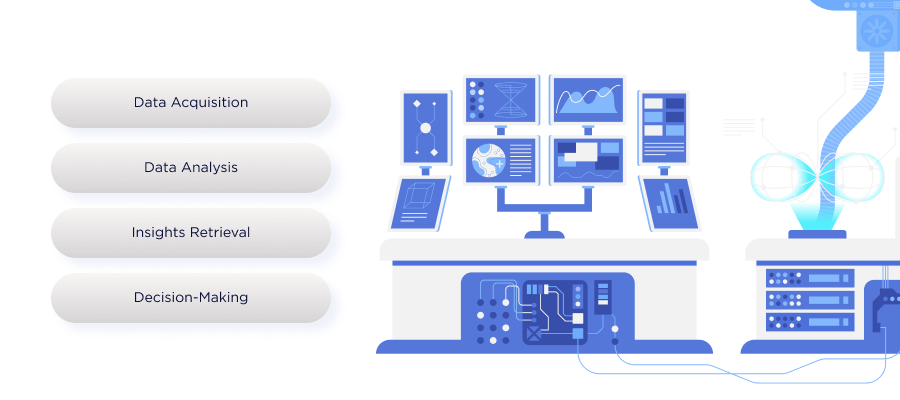
The journey of a smart factory includes a series of progressive stages, each building upon the last to create a fully integrated, intelligent manufacturing environment. This evolution is a technical upgrade and a transformation in how data is utilized to improve business performance. Let’s explore these critical stages in the evolution of a smart factory.
Data Acquisition
The foundation of a smart factory is data acquisition. This stage involves the meticulous collection of data from a myriad of sources — industrial sensors embedded in machinery, production lines, and even environmental monitors. These sensors gather vital information about machine performance, production output, energy consumption, etc. The key to this stage is the breadth and quality of data collected, as it sets the ground for all subsequent analyses and insights.
Data Analysis
With data in hand, the next stage is data analysis. This is where raw data is transformed into meaningful information, often with the use of manufacturing business intelligence solutions. Advanced algorithms and processing tools sift through the vast amounts of data, identifying patterns, anomalies, and trends.
This stage is critical in understanding the nuances of the manufacturing process, pinpointing areas of inefficiency, and identifying potential improvements. Data analysis turns a sea of information into a focused stream of knowledge.
BI for Business
Find out the secrets of how business intelligence boosts operations and what BI tools and practices drive data analysis.
Insights Retrieval
The true power of a smart factory comes to light in the insights retrieval stage. Here, the processed data culminates in actionable insights. These insights could range from recognizing the need for preventive maintenance to optimize machine uptime, to understanding workflow bottlenecks that can be streamlined.
Essentially, this stage is about extracting practical, actionable intelligence from the analyzed data — information that can directly impact the efficiency and effectiveness of the manufacturing process.
Learn more about Preventative Technologies for Supply Chain
Decision-Making
The final stage in the evolution of a smart factory is decision-making. Armed with insights gleaned from thorough data analysis, manufacturers can make informed, strategic decisions. This could involve real-time adjustments to production schedules, long-term investments in new machinery, or changes in supply chain management.
The decision-making stage is where the value of the smart factory is fully visible, as data-driven decisions lead to improved productivity, reduced costs, and enhanced product quality.
If you wonder what technologies help build a smart factory and enjoy better performance, move to the next section and explore what advancements make a difference for manufacturers today.
Essential Technologies in Smart Manufacturing
Smart manufacturing is driven by a suite of advanced technologies. Each technology contributes uniquely, enhancing various aspects of the manufacturing process. Let’s delve into these technologies, their applications, and how they’re reshaping manufacturing
1. IoT Integration
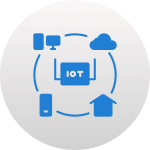
We’ve already mentioned the smart sensors. These are pivotal in monitoring production metrics like temperature, pressure, and speed. Industrial IoT-enabled systems can also predict equipment failures before they occur. For instance, Siemens reduces downtime by 30% through predictive maintenance. This minimizes interruptions and ensures smoother production flows.
Another good example is RFID tags that provide real-time visibility into the supply chain, aiding in better inventory tracking and management. In fact, these tags transform inventory management. According to CosmeticsDesign Europe, Mixer & Pack, a beauty manufacturer, reports that the demand for RFID is growing daily. This technology positively impacts stock management operations as well as the control over unauthorized resale.
Read more about Why You Need to Use IoT in Manufacturing Today
2. Data Analytics and AI
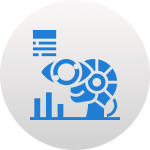
AI and data analytics is another technology that helps with equipment failure prediction in smart manufacturing. AI algorithms analyze data to foresee equipment breakdowns, allowing for preemptive maintenance. For instance, IBM’s AI solutions improve equipment reliability by up to 30% for some clients.
The versatile data analytics toolkit now also offers Generative AI, a more creative companion for manufacturers. It greatly optimizes the work of vehicle designers. For example, Toyota uses GenAI to marry design processes and engineering constraints to make inspiration and technical feasibility get along better.
Other data-oriented technologies like computer vision systems are handy, too. They enhance quality control on production lines by visually inspecting products for defects. These systems analyze visual data with precision and accuracy in identifying imperfections. And ultimately, they contribute to improved manufacturing quality and decision-making processes.
3. Augmented Reality and Virtual Reality
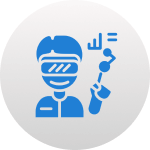
Very popular in retail and entertainment, AR technologies provide interactive maintenance guides for manufacturers. Boeing uses AR to be 40% more productive in wiring harness assembly. AR improves repair accuracy and speeds up the maintenance process.
As for VR simulations, they are not only used to experience the real-life movie. In manufacturing, it simplifies training for workers in complex processes as well as makes it safer. Ford, for example, uses VR to train employees, enhancing safety and proficiency. Besides, VR in smart manufacturing opens more opportunities for remote collaboration among diverse roles within the company.
4. Additive Manufacturing with 3D Printing

3D printing is a new way to make things. Unlike regular ways where you cut or shape something, 3D printing builds things layer by layer using digital models. It lets us be more creative with designs, make prototypes quickly, and create complex shapes that were hard or impossible to do before.
Airbus, a leading aerospace company, has embraced 3D printing to fabricate lightweight and intricate components. This innovative approach has not only significantly reduced manufacturing time but has also led to a substantial decrease in material wastage, as evidenced by Airbus’s adoption of this technology.
And, in the healthcare sector, for example, 3D printing has enabled the creation of custom solutions tailored to individual patient needs. Stryker, a prominent medical technology company, has successfully employed 3D printing to manufacture personalized medical implants. This advancement showcases the potential of additive manufacturing in improving the production of healthcare devices and providing patients with customized and optimized solutions.
5. Advanced Robotics
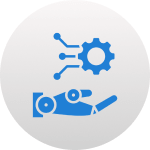
Robots are no longer a thing from the sci-fi. Collaborative robots work alongside human operators and improve overall productivity. Universal Robots, a leading cobot manufacturer, has been innovating in the industry for a while and introduced new 30kg payload cobots just recently.
Besides, the robotic technology is already quite diverse and includes different types of robots such as autonomous mobile robots and AGVs. These robots streamline material transportation in spacious warehouses and relieve people from excessive movement.
Another type, swarm robotics is used for large-scale manufacturing tasks. Such robots work in unison for efficiency and precision. Festo’s BionicANTs demonstrate how swarm robotics can mimic collaborative behaviors in manufacturing.
6. Edge Computing
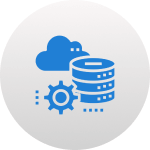
In the context of manufacturing, edge computing involves processing data near the devices and machinery generating that data, as opposed to sending all the information to a remote data center. This shift brings benefits in addressing the unique challenges faced by smart manufacturing processes, such as the need for real-time insights, reduced latency, and improved operational efficiency.
One prominent player in the field of edge computing for smart manufacturing is Intel. Its solutions have shown significant benefits in optimizing the performance of industrial processes. By deploying edge computing technologies, Intel has effectively reduced latency and improved response times in manufacturing settings. This is crucial for industries where split-second decisions can impact overall productivity, product quality, and worker safety.
Explore How to Tackle Time-Sensitive Issues with IIoT Edge Computing
7. Digital Twins
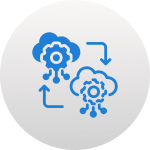
Digital twins are sophisticated virtual models that mirror physical assets, processes, or systems. By taking advantage of digital twins, companies can simulate, analyze, and optimize their products and production processes in a virtual environment before implementing them in the real world.
Siemens again stands among the innovators in the field as a global technology powerhouse. They compose extensive reports on how the technology enables them to test and refine products and processes virtually, leading to fewer prototypes, reduced time to market, and enhanced product quality.
Beyond Siemens, other organizations are also embracing digital twins. For instance, in the energy sector, companies use digital twins to monitor and optimize the performance of wind turbines. This leads to increased energy output and reduced maintenance costs. In the automotive industry, digital twins are used to model and improve vehicle design and manufacturing processes to enhance safety and fuel efficiency.
8. 5G
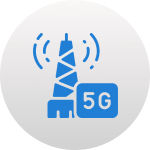
5G connectivity is set to upgrade manufacturing by providing ultra-fast, reliable, and low-latency communication essential for real-time monitoring and control. This next-generation wireless technology enables seamless communication between machines, sensors, and control systems, facilitating more efficient and agile manufacturing processes.
Ericsson’s partnership with Audi exemplifies the potential of 5G in manufacturing. Together, they have explored how 5G can enhance manufacturing applications to increase connectivity and efficiency. 5G’s high-speed data transfer and low latency are crucial for applications such as real-time quality control, remote machine operation, and the integration of augmented reality in production.
5G is also making waves in other sectors. For instance, in many smart factories, 5G enables the deployment of more autonomous mobile robots and drones for material handling and inventory management. In the energy sector, it facilitates real-time monitoring and control of distributed energy resources to enhance grid stability and efficiency.
9. Blockchain in the Supply Chain
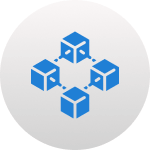
Imagine if you could know exactly where your favorite things come from. Companies like De Beers, who work with shiny diamonds, use blockchain in supply chain to do just that. It’s like a detailed map that shows the journey of diamonds from where they are found in the mines all the way to the store where customers buy them.
Now, let’s think about how manufacturers buy and sell things on the legal side of things. Walmart uses smart contracts based on blockchain to keep agreements up-to-date. These automatically make things happen when certain conditions are met. It helps Walmart manage its processes better, reduces mistakes, and makes communication with partners faster and smoother.
Learn more about How Blockchain-Based Smart Contracts Work Across Industries
10. Computer Numerical Control
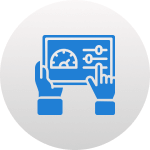
Finally, CNC machining represents a significant advancement in manufacturing technology and offers unparalleled precision and consistency. Computer Numerical Control allows for the automated control of machining tools and equipment, including lathes, mills, and grinders, using a computer and software.
Haas Automation, a leading CNC machine tool manufacturer, exemplifies the impact of this technology. They provide solutions that significantly improve machining accuracy and speed. CNC machining enables manufacturers to produce complex parts with high precision, often with tighter tolerances than traditional methods.
Discover the 16 Core Software Types to Apply in Manufacturing
The future of smart manufacturing technology appears promising, and the current advancements signify just the beginning. The continuous integration of technologies into the work environment holds the potential to yield even more significant positive impacts on businesses in the years to come.
Future Trends in Smart Manufacturing
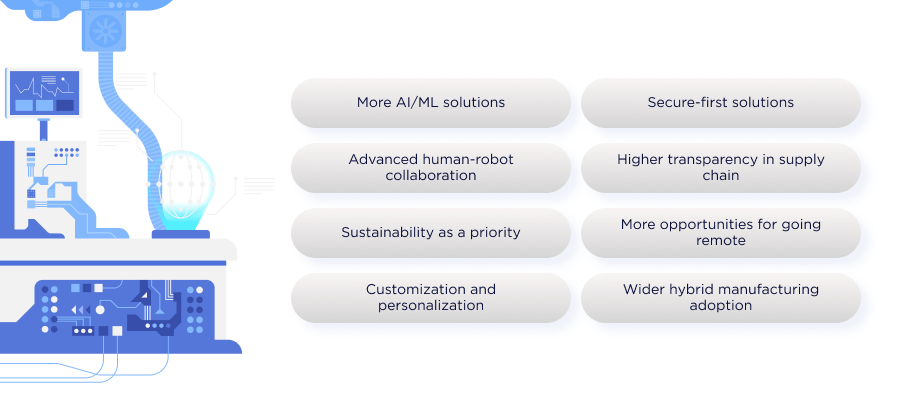
As we stand at the cusp of a new industrial age, the future of smart manufacturing unfolds with a series of trends. These changes are not just technological; they herald a new era of efficiency, customization, and sustainability. Let’s explore these compelling trends that are shaping the future of manufacturing.
Human-Robot Collaboration
The synergy between humans and robots is redefining manufacturing. Collaborative robots, or cobots, are becoming vital in various manufacturing settings, working alongside human counterparts to boost productivity and safety. This collaboration allows for more flexible and efficient production lines, as cobots take on repetitive or hazardous tasks, freeing humans for more complex and creative work.
Hybrid Manufacturing
Hybrid manufacturing represents the convergence of traditional manufacturing methods with cutting-edge technologies. This approach allows manufacturers to harness the strengths of both worlds — the reliability and familiarity of conventional methods with the precision and flexibility of modern techniques.
In highly conservative industries like the medical field, companies don’t neglect traditional machining and stick to what works best historically. On the other hand, the hybrid approach fosters more healthcare manufacturers to innovate and apply such tech as additive manufacturing to create customized implants and prosthetic devices.
Sustainable Manufacturing
Sustainability is no longer a choice but a necessity and even a legal obligation. The manufacturing sector is increasingly focusing on green practices, emphasizing energy efficiency, resource conservation, and waste reduction. This shift towards sustainable manufacturing is not just environmentally responsible, but it also aligns with consumer preferences and regulatory demands, creating a competitive advantage for businesses.
Read more about How IoT Fosters Industrial Sustainability
Customization and Personalization
The future of manufacturing is increasingly customer-centric, with advances in technology enabling greater customization and personalization. This trend meets the growing demand for tailor-made custom software, from car features to personalized medical devices. Manufacturers who can efficiently cater to these individual preferences will stand out in the market. As part of the trend, manufacturers tend to adopt more mobile solutions with appealing user interfaces.
Cybersecurity in Manufacturing
In an interconnected manufacturing environment, cybersecurity becomes paramount. The integration of IoT devices and cloud computing exposes smart manufacturing systems to new vulnerabilities. Thus, protecting sensitive data and intellectual property is crucial. Robust cybersecurity measures will be integral to safeguarding against cyber threats and ensuring the reliability of manufacturing operations.
Learn more about IoT Security Challenges
Supply Chain Innovation
Innovation in supply chain management touches on how products are made and delivered. The blockchain technology and IoT mentioned earlier are creating more transparent, efficient, and resilient supply chains. These technologies enable real-time tracking of materials and products, automate transactions, and enhance supply chain visibility to reduce the risk of disruptions and improve overall efficiency.
Impact on Remote Work
One of the less discussed but significant impacts of smart manufacturing solutions is on the workforce, particularly concerning remote work. Advanced technologies are enabling a more distributed and flexible workforce. Remote monitoring and management of manufacturing processes are becoming feasible, allowing experts to oversee operations from anywhere in the world. This shift expands talent pools, promotes work-life balance, and leads to a more satisfied and productive workforce.
Fuel Your Production with Intelligence
Smart manufacturing technologies are not just reshaping how we produce goods; they are redefining the very nature of manufacturing. By embracing these technologies, businesses can unlock new levels of productivity, quality, and innovation. As we look to the future, the integration of manufacturing technologies will continue to drive growth and competitiveness in the manufacturing sector, heralding a new era of industrial excellence.
If staying abreast of the ever-evolving technological landscape is a challenge for you, don’t hesitate to reach out. We are ready to assess your situation and recommend the most suitable technologies tailored to your specific manufacturing process, products, and end-customer experience.